(Photos by Bob Chiluk, Hot Rod Chassis and Cycle) – It has been a bit of a stretch since we last updated you on Project Violent Valiant, the corner burning, asphalt melting Chrysler powered creation currently under construction at Hot Rod Chassis and Cycle in Illinois. Kevin Tully has been burning the midnight oil on the car and his Miller Dynasty 200DX welder since his return from SEMA and the progress is coming along nicely. Remember, the plan is to have this car up and running around autocross courses in the Spring, so there’s no time for lolly-gagging.
In this installment of the project build, we’re going to watch as Kevin builds the custom rear axle for the car which uses a center section and tubes from Moser as well as Moser axles and Moser’s lightweight aluminum center section to keep the beef to a minimum. Because this car is about a lot more than simply bolting together parts, the rear end is a thing of functional beauty. Kevin has done a bunch of them in this style for customer cars and other builds but good work takes time and from start to finish, we’re looking at an accumulation of about 20 hours work in this piece. How? Why? We’re going to tell you using some great photos from Bob Chiluk and the team at Hot Rod Chassis and Cycle.
In upcoming installments, we’re going to talk about the suspension system, custom rear frame, mounting the axle, and other stuff but for this one we’re simply giving you the straight dope on a piece that seems just way too nice to actually hide under a car. This Valiant will be very well anchored to the Earth. After seeing this Moser rear end come together, you’ll agree with us that Project Violent Valiant is going to be on some sure footing at the track!
SCROLL DOWN TO SEE THIS CUSTOM AXLE COME TOGETHER WITH MOSER PARTS AND HRCC CRAFTSMANSHIP –

Other than the center section and the tubes, every other part of the rear end is hand made by HRCC. Heres an in-progress photo of the lower control arm mounts which are made from 3/16″ chrome-moly steel plate. Dig the hawtness of the welding. Sexy!

Here are the freshly cut side plates before thy were boxed and finish welded.

The upper hole you see is for the control arm mounting bolt to pass through. What are the other holes for? Stand by for that answer.
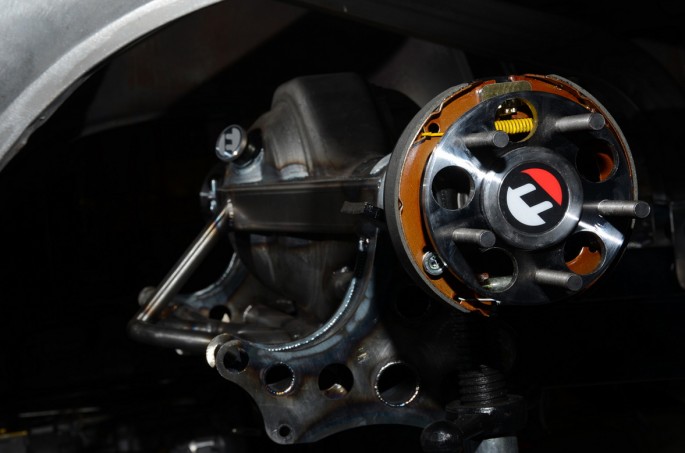
The axles are 35-spline Mosers and they’ll be plenty strong to stand up to the abuse they’ll receive from the high horsepower Chrysler wedge engine that will be powering this car. HRCC uses Moser products exclusively in their builds for good reason. They have a great reputation, killer customer service, and are big supporters of grassroots racing and hot rodding.

There’s going to be a bunch of sexy welding photos in this blog item because that is essentially what this is all about. As you can see here, HRCC has attached a big cross brace, added lots of bracing and mounting brackets to this end of the housing which started life as a plain Moser center section and a pair of loose tubes.

HRCC’s intentions with this design are to remove any and all flex from the rear axle. During launching or hard cornering, housings can do weird stuff and when they do it, the driving dynamics of the car are compromised. The amount of bracing and strengthening here should keep things straight and steady like we want them under the Valiant. Note the hoop and knee brace in the middle of the housing. That’s a tie down point! It is a low point on the car and it will effectively triangulate your straps on the rear end, keeping the car safe during transport on a trailer. We dig this touch! The tubing you see is all lightweight .035 chrome-moly with the intention of getting the strength without causing a weight penalty. With the aluminum center section, this axle is already ahead of where it would be with an iron pig in there.

If we could weld like this we wouldn’t leave the house. HRCC is “powered” by a couple of Miller Dynasty 200DX welders. They are the backbone of the shop and Tully reports that he loves the machines. Obviously the welding machine itself does not produce these results, a skilled operator in conjunction with the welding machine does. That being said, even a great welder can’t perform work like this with a less than stellar unit.

When welding on an axle housing it is super critical to make sure you don’t overheat anything and cause warping or other changes to the piece. All of the work of the additional bracing and brackets would go out the window if the housing itself was compromised. Note the narrow heat signature of the welds and its even color.
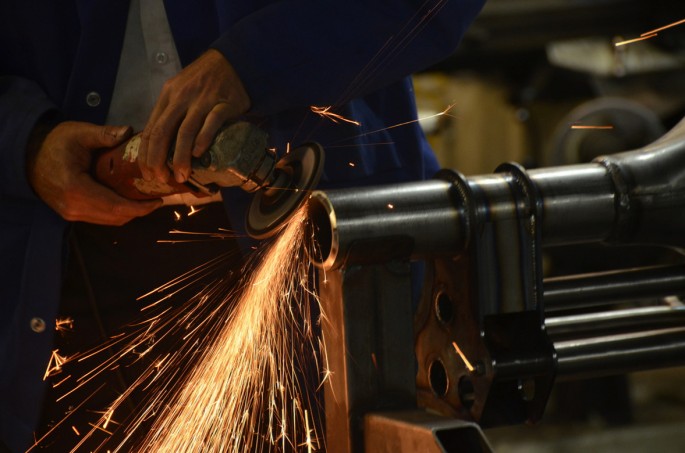
Here we see HRCC’s Kevin Tully dressing the ends of the tubes before adding the Moser housing ends.

You can see Kevin taking a peek here as he welds the housing ends on. The guy could probably do it with his eyes closed but he’s a stickler for quality and these are truly critical welds, so he was taking his time.
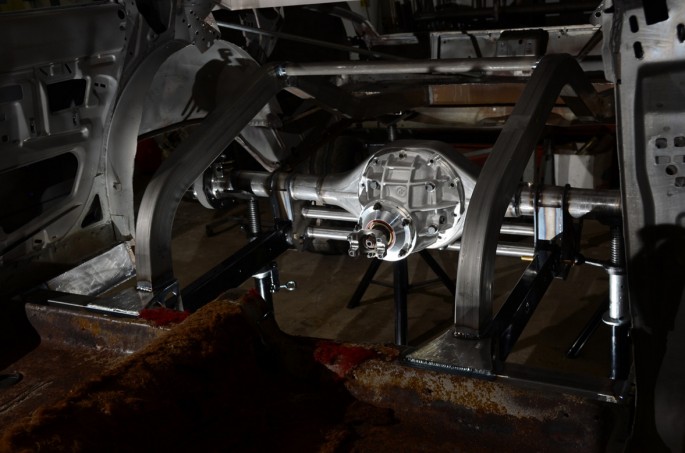
Stuffed full of 3.91 gears and a Moser Wavtrac differential which is capable of handling up to 800hp, this is one fine looking third member. Like the rest of the car, you can see that it isn’t just a drop in piece that was designed to fit the application. The guys are HRCC are really going the extra mile on this car and using the full breadth of their talents along with a full team of build partners who make the best stuff in the industry. We’re getting the foundation of the beast set! Come back next week and we’ll talk rear suspension on Project Violent Valiant!
Click the below links to catch up on the Project Violent Valiant Build!
Project Violent Valiant Introduction
Project Violent Valiant tear down
Project Violent Valiant the car is stripped and ready for the building process
Those welds are works of art!
It simply doesn’t get any better than this…perfect is good enough!
That 8 3/4 is a work of art.
I guess Moser hired some new PR people in the years since my axle broke and ruined my quarter panel and wheel tubb and trunk aluminum! I broke one of their 31 spline axles outside of the bearing letting the wheel/tire/brake drum loose! Their answer,”It was on a drag car”,a 30 over 10 to 1 289 Ford,stock Toploader,3.89 gears on a 10″ M/T ET Street,less than two years old,maybe 25 passes! ROY.
Conversely Roy, I’ve been using Moser components for over 10 years, with only a few projects that had less than 600hp. And I’ve never had one item fail. But, that doesn’t mean I’ll NEVER have something fail from Moser. But I have 100’s of axles that I’ve built, all with Moser components, and when that day comes, I’ll consider all the success I’ve had. Recently, a good friend purchased a set of Strange Axles for his MoPar. And one of them broke on the first launch. Stuff happens. They fixed him up with a new shaft, and he’s had no more issues since.
Finally some photos of a great fabricator who wears the proper gear for welding, not some rat rod hack in a t shirt and shorts. Love the work so far.
I sympathize with Roy, A couple of years ago I had Moser build a set of axles for a full floating rear end, they were so badly engineered that they leaked oil from around the bolts. When asked for help I was told that there was nothing they could/would do. I was able to make my customer happy with no thanks to Moser. Never again, and I will continue to give them all the advertising they paid for.